Introduction
In the data-driven industrial era, precisely tracking the input and output of machines and putting the data into a shared database for analysis is a must for a company to achieve real progress. By lowering human engagement and boosting electronic inputs, this can be accomplished. Stronger demand for personalization, rising customer expectations, and the global supply chain's complexity — these and other issues push manufacturers to come up with new, more innovative ways to stay competitive. Businesses turn to digital transformation in order to boost efficiency and discover new ways to improve manufacturing and supply chain processes. In the manufacturing industry, manually recording accurate downtime and runtime concerns is especially difficult. Adopting the Internet of Things can assist in tracking down and monitoring staff, which could boost manufacturing performance insights.
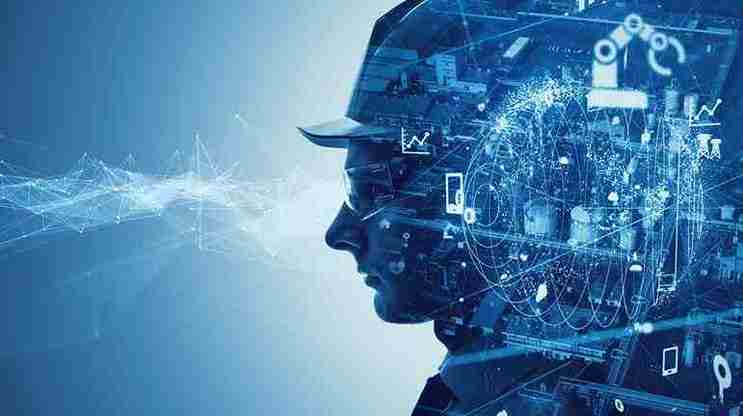
Business Case
In a packaging and printing factory, It was evident that jobs that are currently performed manually might be automated and computerized. It is now difficult to monitor devices manually as there are a massive number of machines in the Manufacturing industries. Business faces problems in run time and in some cases the planup team fails to analyze the problem. When there is no transparency in the factory's operational activities and management, there is no way to estimate costs. In every industrial industry, not only the operation of the machinery is critical, but so is the evaluation of employee performance. Because of this the company is facing numerous losses, limited production and increased time and cost. There have been cases where records for machine downtime and other issues have gone missing; it is critical to keep records in order to address the problem. When the performance level of the machinery is low, there is a huge amount of wastage, which can swiftly lead to the company's demise.
Solution
In the printing and packaging company, SenzMate’s Factoryspy technology will provide the best solutions to measure and provide accurate and reliable data for analysis for the input/output of the reels. This will enable for the extraction and interpretation of waste, work efficiency, effective working time, and other useful data. Following discussions, tablets for each machine have now been added to the scope. Allows Maintenance Service technicians to have a data-driven performance profile. Manufacturers will be able to follow and monitor the operations of maintenance service technicians, such as the number of maintenance issues fixed by individual field service professionals, the overall time taken to resolve the maintenance issue, and the inspection team's validation.
Action Taken
The SenzMate IoT gateway will read the signals from sensors, convert it in readable format and transmit data securely. For managing the remote devices, handling sensors, complex event processing, signal processing and calibration, SenzMate MAGMA IoT platform is incorporated. Completely customizable Threshold-based alert triggering and time series-based data display are provided by the SenzMate User Layer. Two types of sensors can be used to collect the essential data from the machines: an encoder to measure reel revolutions and a proximity sensor to detect cutting. Encoders will be installed in most of the machines to measure the input and output reel rotations. Proximity sensors are only required in the bag cutting machines. Weight will be directly gathered through the weighing machine.
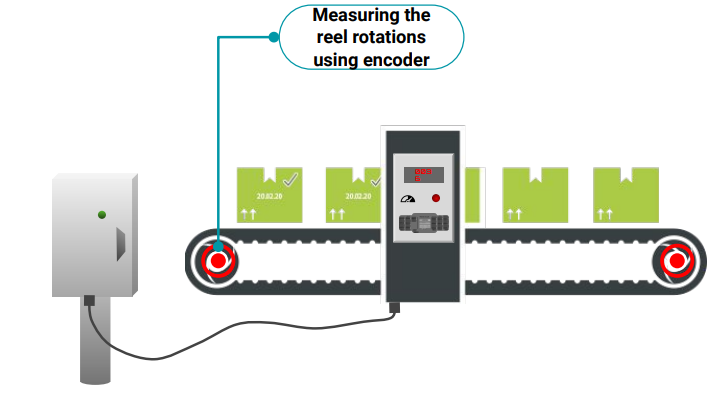
Results
The factory is automated with our SenzMate Industrial IoT solutions, where the requirements of the larger sector manufacturing companies are fulfilled. Measuring the length and width of the output reels where the reel measurements will almost be the same, counting the number of packages, Tablet/Smartphone to enter job details and weight, Dashboard and app management, Collaboration with the existing systems, Report generation. The Industry can improve its Overall Equipment Effectiveness (OEE) by increasing the availability, performance and quality of its production. The solution enables with ecured data transmission, device management, time series based data visualization. When manufacturers use a data-driven performance approach and have such data on hand, they may gain a clear picture of each maintenance professional's efficiency levels. Reward and compensate top performers, and provide skill development training to moderate and low performers, based on the facts. One of the reasons why widespread adoption of Industrial IoT is so wanted is because of these benefits. Many companies in a range of industries are already taking advantage of it.
FREQUENTLY ASKED QUESTIONS
What is Industrial IoT (IIOT)?
The Industrial Internet of Things (IIoT) marks a paradigm shift in industrial operations, transcending mere connectivity to reshape industries from the ground up. Imagine a dynamic ecosystem where sensors, machines, and software interweave, generating a symphony of data that fuels insights, optimizes processes, and drives informed decision-making. This is the essence of IIoT, a catalyst for unprecedented efficiency, productivity, and safety in the industrial landscape.
What are the benefits of using Industrial IoT in the industries or factories?
The adoption of Industrial Internet of Things (IIoT) in industries and factories brings about a range of transformative benefits. IIoT enables real-time connectivity and data exchange among industrial devices and systems, enhancing operational efficiency and productivity. Through the integration of sensors, actuators, and smart devices, industries can achieve predictive maintenance, minimizing downtime and optimizing equipment performance. The ability to gather and analyze vast amounts of data facilitates informed decision-making, leading to improvements in process optimization, resource utilization, and overall operational effectiveness. IIoT also supports remote monitoring and management, allowing for better control of industrial processes and equipment. This connectivity and data-driven approach not only streamline operations but also pave the way for innovations in automation, supply chain optimization, and enhanced safety protocols, ultimately contributing to a more agile, efficient, and competitive industrial landscape.